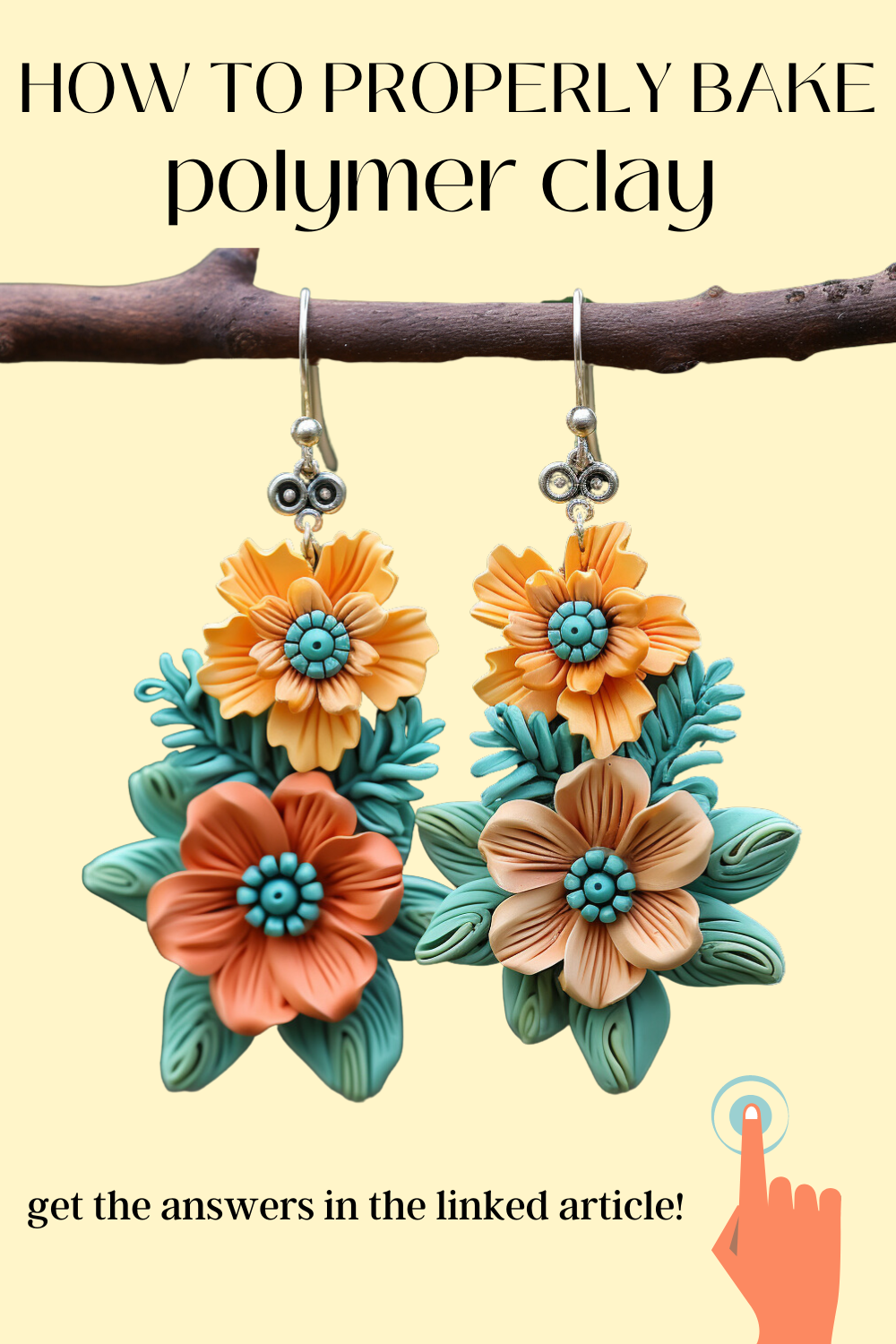
How to properly bake polymer clay and know that it is done and cured
This is the simplest thing to answer, but one of the most often asked questions!
READ THE PACKAGE AND DO WHAT IT SAYS. This is the number one tip we can give you. The clay has chemicals and composition that are created in a factory by people who understand plastics- and the best way to properly cure it is to follow the directions. Don't make up your own time or follow advice from someone you just met on TikTok for "baking for HOURS at a low temperature." This is not good advice and your clay will fall apart later.
For our favorite clays from Sculpey, which are Premo and Soufflé, (Sculpey original and Sculpey III too) the bake time is 30 minutes per 1/4" of thickness, at 275 Farenheit. Simple- just bake it for half and hour in an oven you have TESTED so you know it is maintaining the temperature.
The most seen results from baking for too short of a time at too low a temp is that your clay will crack and fall apart.
Polymer clay is non-toxic. It is safe to bake in an oven that also makes food. It may create a "smell" and this is just from the off-gassing during cooking, it is not a toxic fume. There is a LOT of misinformation on the internet.
Some tips to take your baking further:
ALWAYS, every time, bake the whole piece for the recommended time and temperature. Do not "partial bake" and it's 100% ok to rebake your pieces multiple times.
You can "tent" your piece. This means put it under aluminum foil or a pan flipped over. Reasons to do this include trapping the smells, and protecting from the heat elements in the oven which cycle on and off. This is especially important if you use a small oven or toaster.
You can bury your piece in cornstarch. Bake for twice the time, so that the entire piece reaches and stays at the curing temperature. Reasons to do this include protecting light colors such as white, beige, and translucent.
You can support your large, curved, or delicate piece with fiber batting, cardboard, aluminum foil, silicone molds or pieces, balled up paper, anything that will go into the low temperature - none of these items will burn when properly placed on a baking sheet away from the oven elements.
You can bake on unglazed (not shiny) tile, silicone or teflon baking sheet, paper, card stock, index cards- this will protect the back of your piece from getting shiny which will happen on a glazed tile, metal bake pan, or glass surface.
THE "BEND TEST:"
SOME polymer clay will bend after being properly cured. Premo is one of them, Soufflé, Kato, Cernit, and Fimo Professional too. NOT ALL clays are meant to bend, so if you see someone doing the "bend test" online and they try to tell you "all clay should bend after baking" they are incorrect.
Do not do this test on fresh hot baked clay. Most brands will just completely fail during a hot bend test. Let it cool.
Do NOT bend test EVERY thing you bake. The purpose of this test is to make sure your oven is working properly, the clay you are using is coming out cured properly, etc. The only reason you want to even do this test is to confirm all your settings are correct for your clay. (It baffles us that people on videos are showing a bend test on every thing they pull out of the oven).
Mixing clay brands:
If two clay brands have a very wide spread between baking temps, I don't mix them. The clay needs to reach the full temperature for the full time. Most clay will scorch if you bake it too high, and it will come out uncured if you bake it too low. so if one bakes at 230 F and the other at 275 F, I would call them incompatible for mixing. A clay that bakes at 265 can survive the extra 10 degrees.
Bake mixed brands at the highest temp and longest time recommended on both packages.
The exception is Liquid Clays. Most need to reach 300F for a few minutes to cure. The best way to use them then is to bake the main clay for the appropriate time at temperature, then raise the temp to 300F for 10 minutes to finish it off, and watch carefully so it doesn't scorch. If you use liquid clay as a surface sealer, you may want to finish it off straight from the hot oven with a heat gun. This gives a gloss finish to the coating and makes it look like resin. This must be practiced as it takes some finesse to raise the temperature without burning the clay.